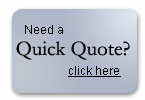
|
Process Control for Scrap Metal and High Temperature Scrap Metal Production
|
Production of our high temperature scrap metal and alloy scrap begins with our experienced metal sorters' sorting through each piece to determine the alloy designation by spectrographic examination, using the Fuse and/or Spectrotest computer analysis. We calibrated our analytical equipment to only known reference standards and very narrow control limits are imposed on each element. Whenever necessary, we send material samples to an independent laboratory for verification to ensure all trace elements meet specific customer requirements. Precise compositional analysis using the most cost efficient method is the cornerstone of our business. This is an essential ingredient in providing our customers with the highest quality raw materials produced at the lowest possible cost. The material is then custom cut to customer specifications by the appropriate inhouse method: bandsaw, plasma torch, one of our nine hydraulic shears or cobbled in our shredder fitted with a custom automated feeding system. Depending on the product and its condition, the material is washed, degreased, chemically milled or shot blasted in one of our five inhouse wheelabrators. Our inhouse processing controls enable us to supply a superior surface finish and exceptional dimensional control. Finally, the finished product, whether it's nickel scrap, cobalt scrap, or Titanium scrap, is placed on a shaker table for another close visual, chemical and dimensional inspection, to insure 100% compliance with the order specification before being placed into the desired packaging.
Contact Monico Alloys to learn more about how our Process Control helps us provide the some of the best high temperature scrap metal and high temperature alloy scrap on the market.
|
|
|